In the selection of vibrating screen models, a lot of data is necessary and will have a huge impact on the results, so we need these necessary data.
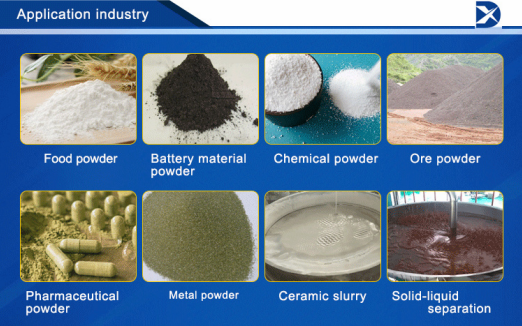
Material Name:
The name of the material is necessary information. After knowing the name of the material, you will quickly find the material’s physical properties, chemical properties, fluidity, whether it contains oil, whether it contains static electricity, whether sealing measures are needed, and the material selection of the vibrating screen.
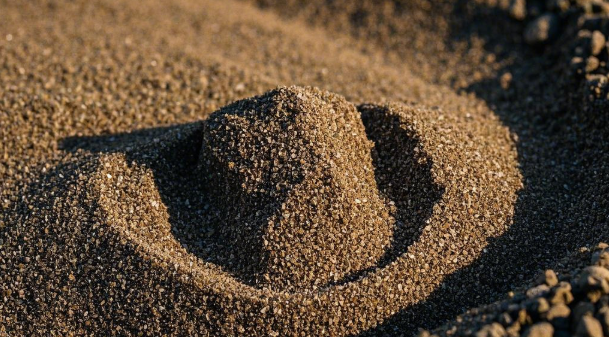
What needs to be screened is petroleum fracturing sand, which means that the bulk density is between 1.5-2.0. The vibrating screen is made of carbon steel, non-acidic, non-toxic, oil-free, and static-free. The mesh size is usually 20 mesh, 40 mesh, 70 mesh, and 120 mesh. The net cleaning method is a bouncing ball. The precision requirement is very high, and it needs to reach 99%. It is used in oil extraction work. According to previous experience, the 2040 square gyratory screen has an output of 6-8 tons per hour.

The material to be screened is flour, with a bulk density of about 0.5. Flour is non-acidic, non-toxic, oil-free, and has a small amount of static adsorption. Flour is food, so food-grade materials must be selected, 304 or 316 stainless steel, silicone seals, and all screen cleaning devices are made of silicone. Usually, flour is selected with 24 mesh, 40 mesh, 60 mesh, or 80 mesh depending on the purpose. In particular, in order to prevent dust explosions, customers are advised to choose explosion-proof motors. According to previous experience, a one-meter Straight row sieve or rotary vibrating screen with a 60-mesh mesh can produce about 500 kilograms per hour.
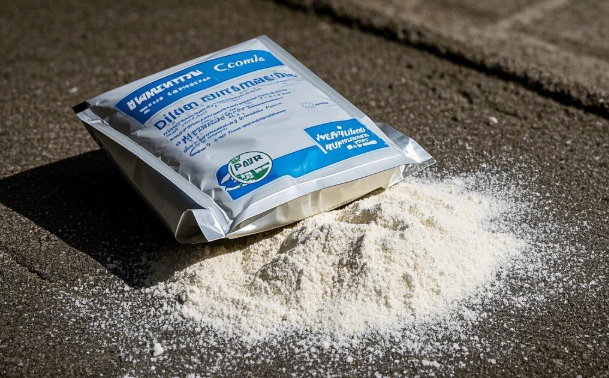
The first thing to pay attention to when it comes to pesticide powder is whether it is toxic. The vibrating screen must be fully sealed, and some highly toxic powders must be pressure tested before leaving the factory to ensure that there is no leakage. Secondly, we must consider the pH value of the pesticide powder, the degree of corrosion to the equipment, and whether to replace it with a more corrosion-resistant material. At the same time, full welding on both sides must be achieved. The third issue is the sealing of the feed port, discharge port, and upstream and downstream equipment. Or some materials cannot come into contact with oxygen, and it is necessary to add an inert gas inlet. Some materials cannot come into contact with metal, so we will spray a Teflon layer inside the equipment to ensure that the material does not change its properties, etc.
In general, the name of the screening material is very useful and meaningful for the selection and non-standard customization of screening equipment.