An American company specializing in creating high-quality acrylic powders for a diverse range of cosmetic products faced steadily increasing demand. To meet customer requirements, we provided an ultrasonic vibrating sieve to improve the screening efficiency of their acrylic powder.

Customer Requirements
Output: Hourly output ranging from 100kg to 200kg.
Mesh Sizes: Screening at different mesh sizes (106 microns, 90 microns, and 75 microns).
Material Specifications:
The specific gravity of acrylic powder is approximately 1.2-1.8.
Good fluidity.
Machine base material: Carbon steel.
Contact material: Stainless steel.
Number of Screen Layers: 3 layers.
Screen Mesh Sizes: 104 microns, 88 microns, 74 microns.
Capacity: 100kg/h to 200kg/h.
Customized Solution for Enhanced Productivity
After discussions with the company’s technical staff,
we recommended an ultrasonic vibration sieve
machine with the following specifications:
Diameter: 800mm.
Layers: 3 layers.
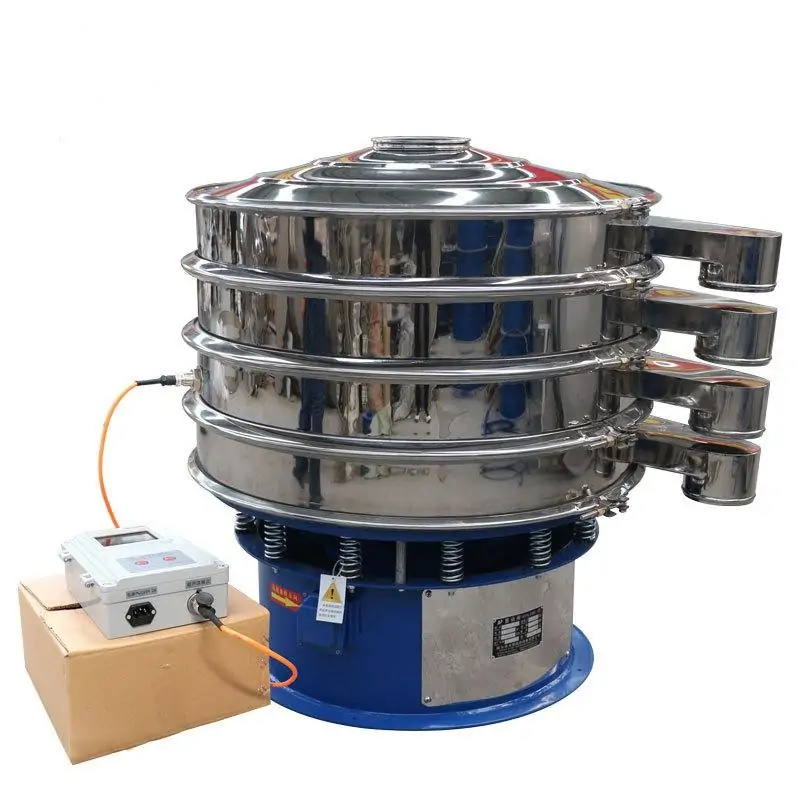
75 Microns: Ultrasonic Assistance
For the 75-micron mesh size,
ultrasonic vibrations were used to gently nudge finer
particles through the screen mesh, ensuring thorough and accurate separation.

90 Microns and 106 Microns: Bouncing Ball Mechanism
For the 90-micron and 106-micron mesh sizes, a bouncing ball mechanism was introduced. This mechanism effectively separated larger particles through the bouncing action of balls against the screen, enhancing screening efficiency and minimizing mesh clogging.

Results
The ultrasonic vibrating sieve adopts a three-layer design, ultrasonic assistance, and a bouncing ball mechanism, enabling the company to achieve the desired hourly outputs of 100kg to 200kg while consistently meeting the specified needs. This solution significantly improved the screening efficiency and productivity of their acrylic powder processing.